Having collaborated or/and developed Products across various industries for Companies ranging from startups to SMEs and Fortune 500 in Asia, Europe and N.America, in a series of 7 posts, we share Factors we experienced and affected our Design and Product Development processes.
Here, in our 4th post, we focus on “MANUFACTURING & PRODUCTION”, as we move from the world of dreams to reality.
Here, in our 4th post, we focus on “MANUFACTURING & PRODUCTION”, as we move from the world of dreams to reality.
disclaimer: The examples presented below are nor Projects/Products 03 designed/developed unless otherwise stated. All rights remain with their owners.
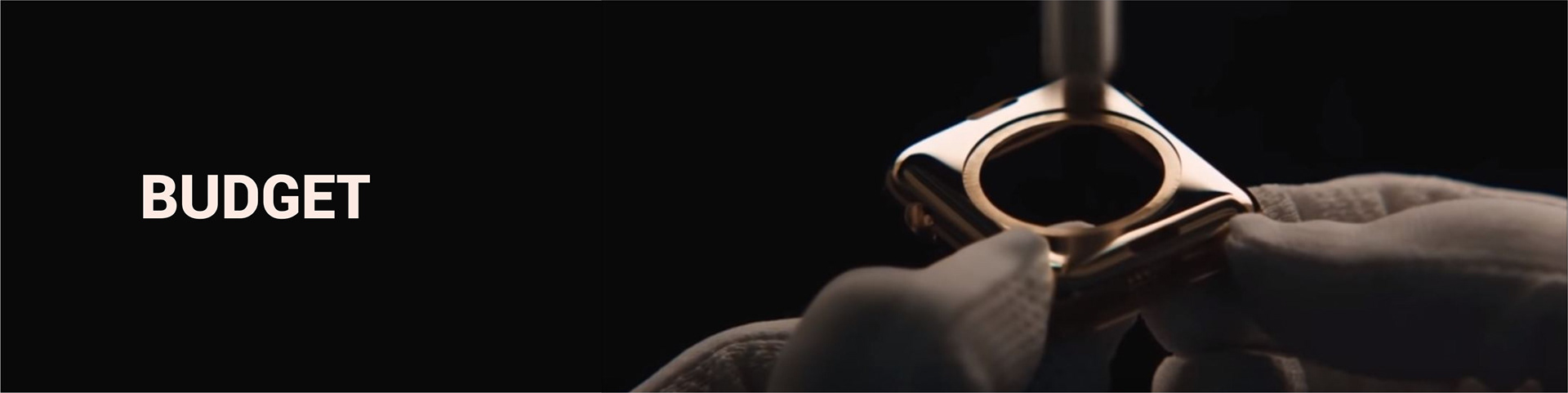
BUDGET - Every line, every curve, every gap, every material/color choice, all have a cost. Yes, we know, all designers, startups (or even established companies) would like their new wearable device to be comparable or even better than Apple’s Watch. Unless you, as a designer, entrepreneur or Organization having a valuation of around 1 trillion dollars to invent and patent new materials, invent and patent new production and assembly methods, develop custom tooling and source contract manufacturers willing to adjust their production processes to fit your specifications, then perhaps your Product will need to be redesigned to fit real-life Product development scenarios. Designers and Development Teams is of paramount importance to be able to design and develop based on realistic financial constraints.
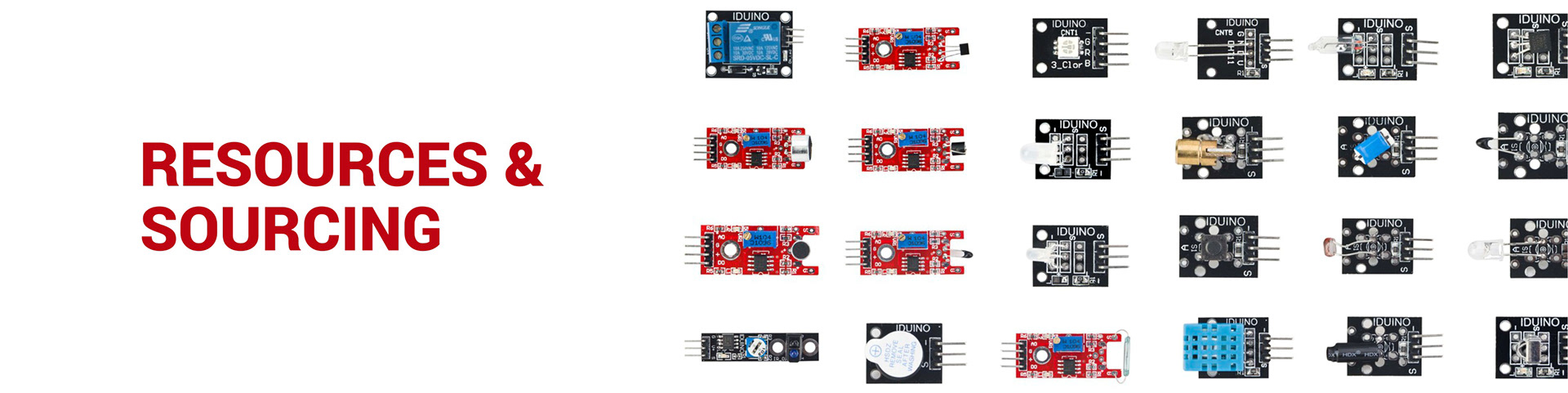
RESOURCES & SOURCING - Developing a Product without being able to source critical skills for its manufacturing (ex. Engineers, Craftsmen), materials, components and manufacturer is, as airlines would say, trip in vain; a trip that will be so delayed that it pointless eventually to take.
Early on the Designers and Development Team need to put down the resources the Organization has or can get and only then start developing any Product. These resources set the framework and limitations within a Product will be developed. Failing to do so and moving on the development process only to find out that the supply chain is missing a link it is a huge waste of time and money. In this case though, there is no refund.
Early on the Designers and Development Team need to put down the resources the Organization has or can get and only then start developing any Product. These resources set the framework and limitations within a Product will be developed. Failing to do so and moving on the development process only to find out that the supply chain is missing a link it is a huge waste of time and money. In this case though, there is no refund.
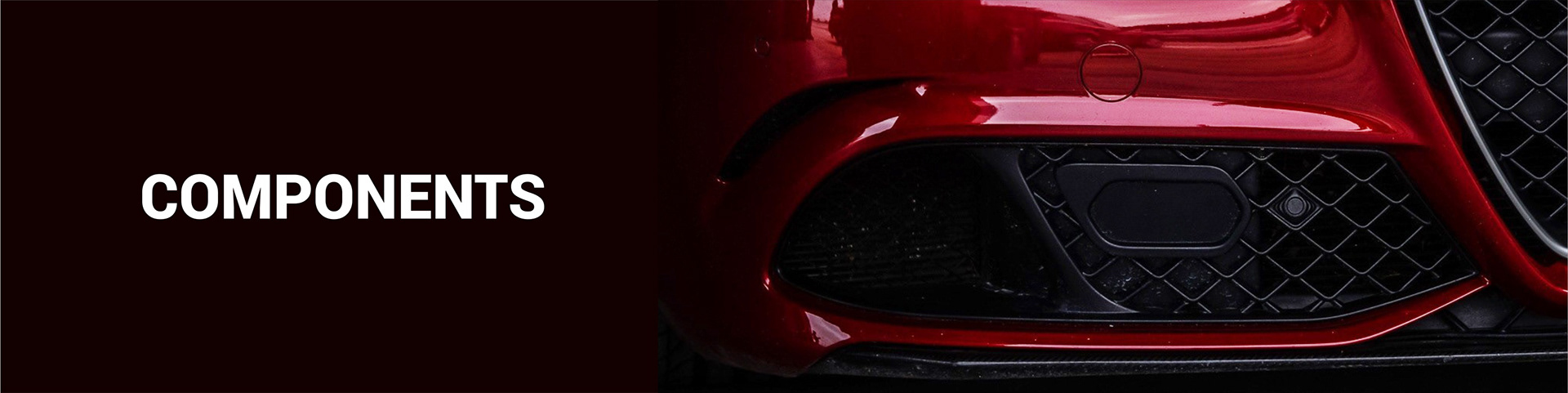
COMPONENTS - Components rule. They are the dictators of a Product. It is them that they determine for example a Product’s architecture-layout (such as on-screen cameras that now allow bezel-less phones), size (such as battery size), appearance details (such a visible screw heads) and so on. A Designer’s and Development Team’s role actually is to respect these Components and “shape” the Product around them to the extent they are allowed.
Look for example the grill pattern in the lower part of Alfa-Romeo Giulia’s front bumper. Maybe you can distinguish the dot-like sensor components in the left and right of the V-shaped grill. It is the size of the these sensors that dictated the size and spacing of this simplified honeycomb grill. And look at this awkward-looking bigger hexagonal sensor component, how its size (dictated by the internal components) is not matching the grill’s grid. A fight to balance restrictions and visual balance, that in this case seems lost.
Look for example the grill pattern in the lower part of Alfa-Romeo Giulia’s front bumper. Maybe you can distinguish the dot-like sensor components in the left and right of the V-shaped grill. It is the size of the these sensors that dictated the size and spacing of this simplified honeycomb grill. And look at this awkward-looking bigger hexagonal sensor component, how its size (dictated by the internal components) is not matching the grill’s grid. A fight to balance restrictions and visual balance, that in this case seems lost.
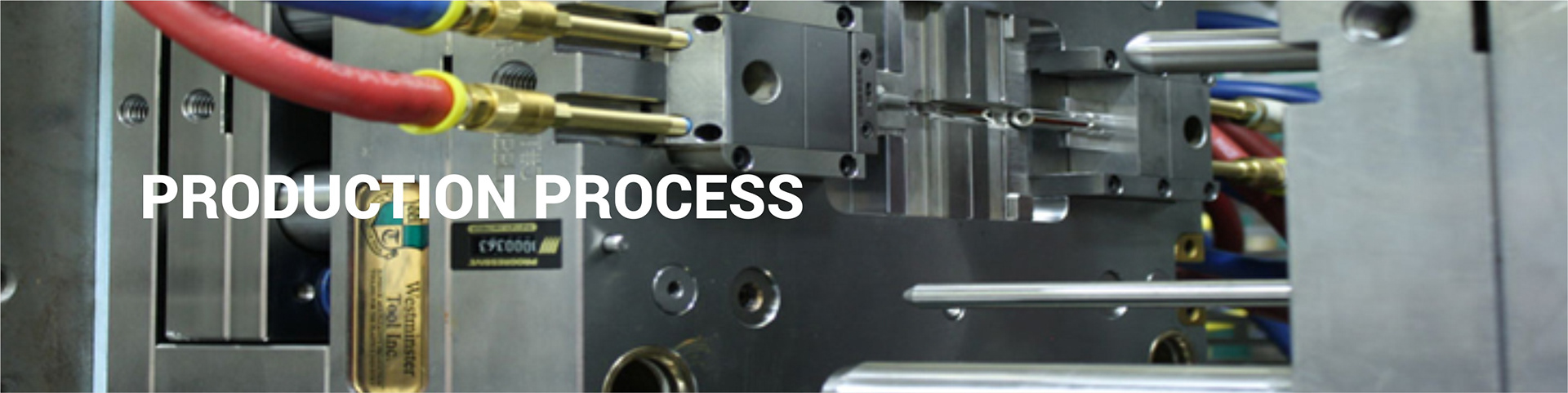
PRODUCTION PROCESS - Choosing the appropriate Production Process for a Product is a kind of chicken and egg situation. Design may dictate the Production Process or the later may dictate the Design. In both situations, both factors will have to be in absolute accordance as they will highly affect each other. Usually, aspects facilitating any decision in this section are the production quantity, resources available, budget and aesthetics-visual requirements. As the cosmetic, functional and engineering limitations and requirements that each Production Process poses are completely different, Designers and Development Teams have to make critical decisions very early on the development process.
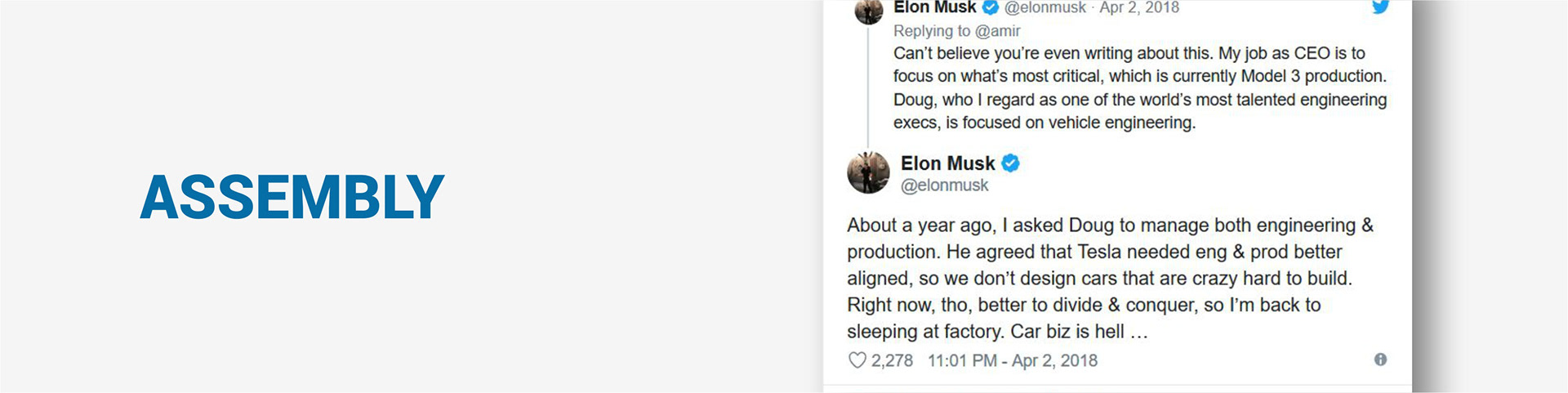
ASSEMBLY - There is this notion that an industrially, mass-produced product is magically constructed inside a production plant, packaged and ready to be shipped. To the great surprise of many, please let us inform you that the industrial mass-production is a highly manual operation that requires dexterity, focus, precision and speed. Therefore, Designers and Development Teams when designing a Product have to consider who and where will assemble the Product and Design-for-Assembly (DfA) accordingly.
It is common secret that Elon Musk downplayed the importance of Assembly processes in Tesla’s Factory, an attitude that directly affected Tesla's cars production speed and Product quality.
It is common secret that Elon Musk downplayed the importance of Assembly processes in Tesla’s Factory, an attitude that directly affected Tesla's cars production speed and Product quality.
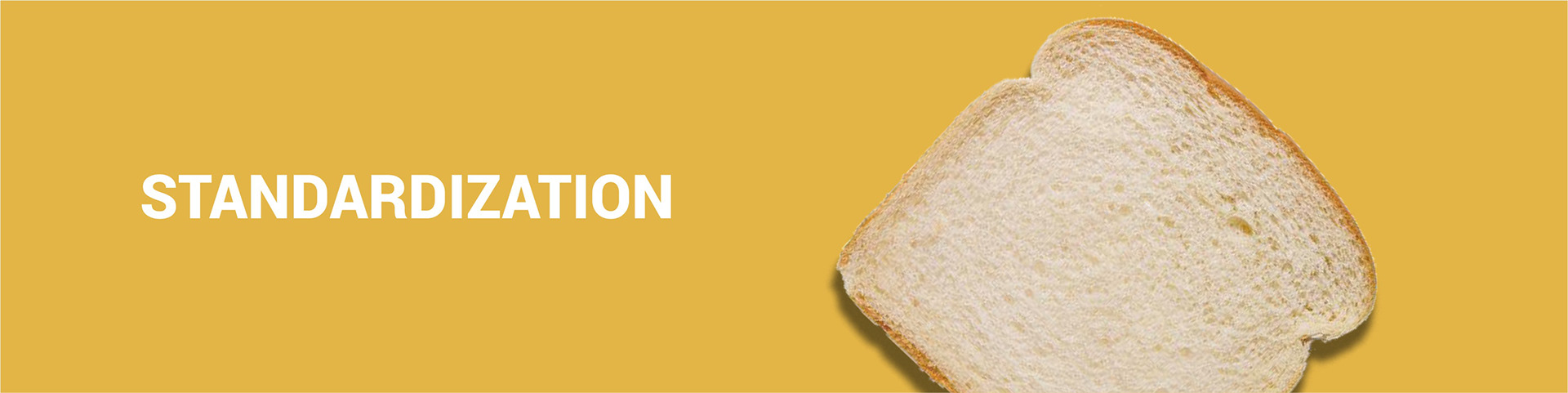
STANDARDIZATION - It took humanity about 12.000 years to transform a loaf of bread from a handmade process to the gold standard of mechanization and (expectedly) standardization; the sliced bread. Yet, today, in the pinnacle of Industry 3.0, now moving to 4.0, there are Organizations, Designers and Development Teams that neglect the collective efforts of the global industrial community to set standards in processes and components that allow cost savings, speed, availability, quality and safety. Standardization is perhaps what allowed the technical and financial viability of the majority of the products we enjoy today. Common and interchangeable parts enabling Product variety and flexibility. Designers and Development Teams ought to know their industry standards and design their Product in ways so that they comply with as many as possible. The examples of failed Products of Fortune 500 companies and startups that tried to deviate from standards for the sake of mere “innovation” are numerous.
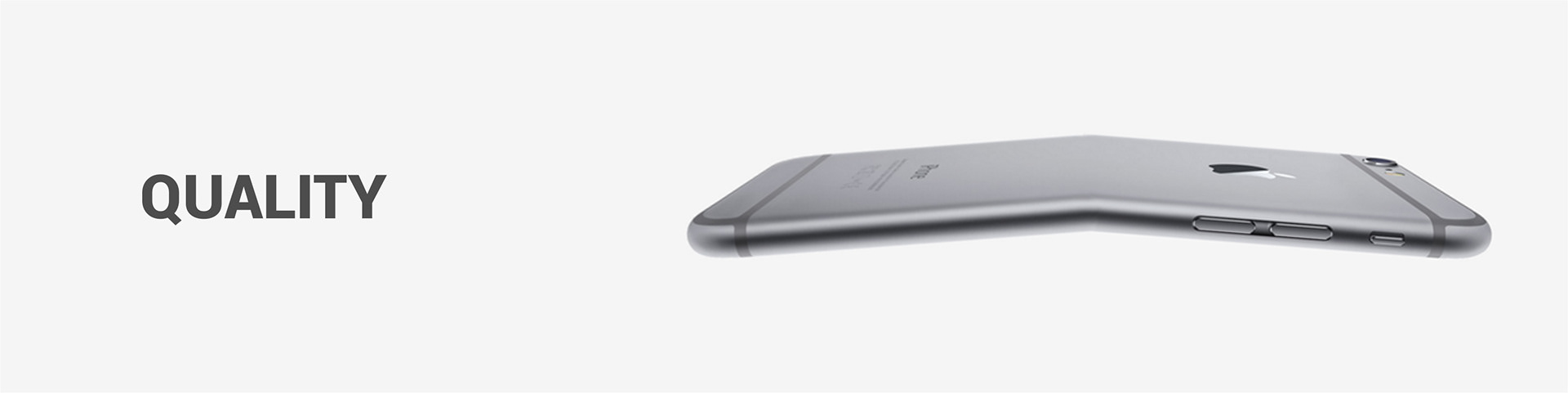
QUALITY - The common denominator of what is discussed until now, is Quality. Whether is the intangible perceived brand Quality, the tactile one when using the Product, or the measurable ones related to durability, low defect rates in production and dead-on-arrival numbers, Quality is the main consideration for all Product stakeholders. For this reason, Product design and development decisions have to constantly reflect to the Organization’s set Quality standards.
In the past few years we all read (some may even experienced) of smartphones bending and exploding. These Products came from Organizations with serious Design, Engineering and Manufacturing skills, yet, somewhere down the development process, trying to balance Design, Engineering, Cost and Lead-Time decisions, Quality was sacrificed.
In the past few years we all read (some may even experienced) of smartphones bending and exploding. These Products came from Organizations with serious Design, Engineering and Manufacturing skills, yet, somewhere down the development process, trying to balance Design, Engineering, Cost and Lead-Time decisions, Quality was sacrificed.